Production supervisor Scott Wagner received a text message at 6:42 a.m. while at home preparing for his commute. The night shift ended almost two hours ago, but he was just now learning about a critical failure in the assembly line’s main conveyor system. The overnight team had been struggling with the issue since 4:15 a.m., but without direct communication channels, the information had to pass through several people before reaching him.
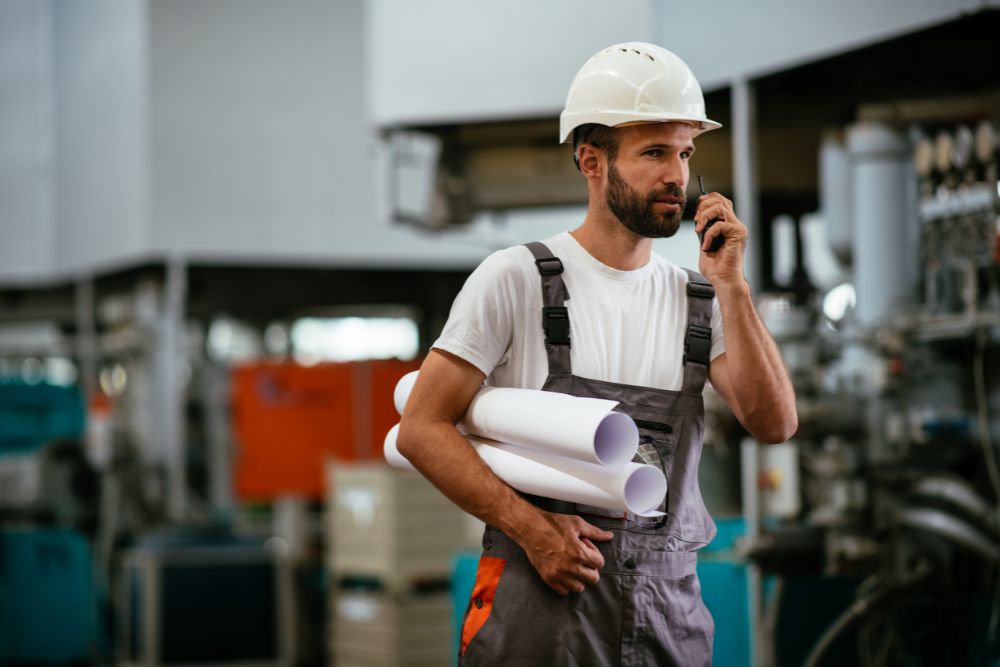
When the conveyor line first began to slow, the line workers immediately noticed the issue and looked around for their supervisor, but he was nowhere to be found. With no supervisor present and the maintenance person with the lone walkie-talkie also absent, someone had to physically search for help in the vast facility—a building that takes 15 minutes to walk end-to-end, or half that time at a slow jog.
Thirty minutes later, Wagner arrived on the facility floor and found three maintenance technicians debating the proper troubleshooting sequence. At the same time, the entire day shift production staff of 135 stood idle. The confusion had already cost the company over four hours of production time, amounting to approximately $20,000 in lost output, excluding additional labor costs. What made the situation particularly frustrating was that everyone involved had done their best within the constraints of their roles.
The information had traveled up through team leads to supervisors, managers, and back down again—but this hierarchical communication path had transformed what should have been a 30-minute fix into a half-day crisis. Without effective communication tools distributed among the team, a minor technical issue had escalated into a major production delay that would impact delivery schedules and production targets for the entire week.
The Impact of Hierarchical Communications
This scenario plays out in manufacturing facilities every day. A small mechanical issue spirals into productivity issues when workers can’t quickly alert the right people. Line operators notice problems immediately but face a painful choice: abandon their stations to search for help or watch as production grinds to a halt.
Maintenance technicians with specialized knowledge are often unreachable in distant parts of the plant. Supervisors learn about critical failures hours after they begin. Meanwhile, frontline workers stand by watching the clock and company profits tick away. The problem isn’t worker dedication or technical skill—it’s communication infrastructure that traps vital information within departmental silos and forces physical messengers to run through vast facilities when seconds count.
In manufacturing environments, hierarchical communication bottlenecks create silence. When information must crawl through rigid chains of command, problems that workers could solve in minutes fester for hours. Line employees spot issues immediately but lack direct access to decision-makers, forcing them to physically hunt down supervisors through sprawling facilities. This communication paralysis transforms minor technical hiccups into production nightmares, with entire crews standing idle while messages slowly make their way through organizational layers.
The real cost isn’t just in lost output and revenue—it’s in the frustration of workers who recognize problems but remain powerless to address them. Each time a maintenance issue requires a worker to leave their station to find help, the company loses efficiency while reinforcing a culture where those closest to the problems have the least ability to solve them.
The Power of Universal Communication
In progressive facilities, a transformational approach equips every frontline worker with smart communication devices—not just select staff and management. This democratization of communication tools creates an environment where issues are reported and addressed in real-time, bypassing traditional hierarchical information flows that can delay resolution.
When every employee has direct communication capabilities, they can instantly connect with maintenance, safety personnel, or management without needing to search for a supervisor or rely on others to relay messages. Smart radio devices also offer instant translation capabilities using artificial intelligence (AI), allowing workers who speak different languages to communicate effortlessly, turning potential barriers into seamless collaboration.
The efficiency gains are substantial. A study by Quickbase claims that more than half (53%) of employees say they spend over 10 hours per week searching for information they need from different people and systems. For 22% of people, chasing information takes up more than 20 hours of their workweek, according to the report.
Beyond immediate operational benefits, universal communication generates valuable data. Analytics reveal communication patterns, helping facilities managers identify recurring issues, communication bottlenecks, and opportunities for process improvement.
Cross-Departmental Coordination
When departments operate in communication silos, facilities face significant risks. A maintenance issue can quickly escalate when operations teams are not immediately informed, or safety hazards may persist because cleaning crews cannot directly alert the appropriate personnel.
Smart communication devices deployed to every worker help bridge these departmental divides. When maintenance technicians discover an equipment malfunction, they can instantly alert operations, safety, and management, reducing response times.
The ability to create dedicated permission-based channels transforms collaboration without creating a communication overload. Maintenance teams can establish specific channels for electrical systems, safety, HVAC, or plumbing issues, ensuring specialists receive only relevant communications while maintaining an all-facility channel for broader concerns. Plant managers can also gain remote visibility through smartphone integration on these same on-site radio channels, allowing them to make informed decisions from anywhere.
Top American Apparel Maker Transforms Distribution Center Communication
One of America’s leading basic apparel manufacturers embraced the universal communications approach, significantly improving its operations. Its challenge was substantial: managing two adjacent distribution centers spanning 1 million square feet with roughly 600 associates using an outdated communication system that limited connections to around 50 devices on shared channels.
The company implemented over 200 smart radio devices across departments to dramatically expand communication access for employees, resulting in immediate improvements in workflow efficiency. In particular, their team created specific channels for specific departments, such as warehouse operations, value-added services, maintenance, and security, while maintaining direct one-on-one communication capabilities when needed.
This democratized communication approach eliminated the previously existing hierarchical barriers, where only supervisors had communication tools. By extending advanced communication devices to frontline workers who previously operated without them, the company fostered greater engagement and empowerment among its team. The company observed increased initiative and accountability on the floor, demonstrating how smart communication technology can transform operational efficiency and organizational culture simultaneously.
Managed Services Model Advantage Drives Lower Total Cost of Ownership
Unlike traditional walkie-talkie purchases, smart radio deployments can be purchased as a service, eliminating upfront capital costs for communication systems. Facilities managers now gain access to enterprise-grade communication technology with predictable monthly fees covering hardware, software updates, and maintenance. As needs change, facilities scale by adjusting subscriptions instead of buying more equipment.
A five-year cost analysis shows that facilities can save $330,000 to $680,000 by deploying 100 smart communication devices on a managed service model compared to purchasing traditional walkie-talkies. Additionally, with upgradable software-based smart devices, organizations automatically benefit from new features and capabilities over time, which boost operational efficiency without requiring additional purchases.
Universal communication tools deliver measurable ROI through faster problem resolution, enhanced safety outcomes, and a more engaged workforce. By eliminating information hierarchies, facilities create agile operations where every employee contributes to the company’s overall success. Forward-thinking facility leaders must evaluate their current communication infrastructure and ask, “Is our established communication infrastructure enabling the workforce to connect, collaborate, and contribute?”
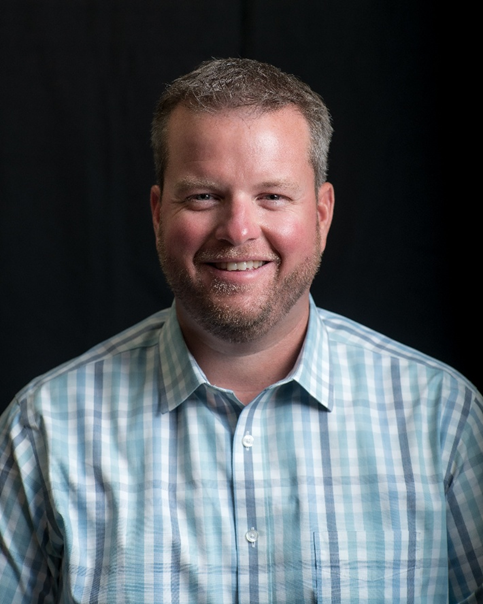
Kevin Turpin is the founder and CEO of weavix, a company focused on transforming industrial worker communications through frontline technology.